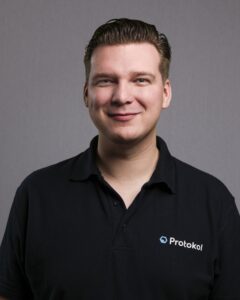
By Lars Rensing, CEO of Protokol, DPP Solution Provider
The European Union’s Ecodesign for Sustainable Products Regulation entered into force in 2024, and over the course of the year, many SMEs became aware of the impact heading their way. The regulation – which aims to make ‘sustainable products the new norm in the EU’ – puts a real focus on product longevity, energy efficiency, ease of repair, and recycling, relying on access to data on product lifecycles across the supply chain to support this.
Core to the regulation are Digital Product Passports (DPPs) which have been mandated for compliance. DPPs are digital records of a physical product that securely and concisely keep track of event, transactional, and sustainability-based information across an item’s lifecycle. The mandate will apply to SMEs and all businesses that place products from specified product groups on the European market – this will include product groups within the electronics, textiles, and furniture sectors, with many more also being targeted.
This legislative move will prove vital to the EU’s ambition to promote environmental sustainability and help the circular economy to grow, but it will also mean a huge undertaking for businesses it impacts, especially for SMEs that don’t have unlimited resources to pour into new technologies or operational processes to get up to speed.
The first and most critical step for SMEs who want to comply involves identifying and validating the necessary product and environmental data to inform the new legislation’s mandate.
While specific requirements applying to each industry are yet to be announced (via the delegated acts), and the European Commission having stated that they will provide SMEs with some level of support for compliance (currently TBD), SMEs risk being caught on the backfoot if they don’t proactively take initial preparation into their own hands.
As this process will be complex, a proactive approach to data collection and validation is essential for companies to establish a robust strategy for complying with the ESPR’s mandate for DPPs.
The following steps provide a clear pathway for preparing your SME for the DPP mandate.
Getting key stakeholders on board
Businesses should begin by aligning closely with stakeholders across the supply chain, such as suppliers and logistics partners. This collaboration is crucial for a holistic understanding of the available product data.
SMEs might not have the resources available for a dedicated ESG function, therefore employing ESG or DPP consultants to help conduct a DPP Readiness Assessment, DPP workshop or consulting is particularly beneficial.
Taking stock of available data
It’s recommended that SMEs conduct a data gap analysis on existing data, focusing on the elements likely to be required in a DPP. An example of this would be data on waste generated during the production of a particular product. This analysis will help identify gaps in product environmental data, allowing organisations to determine how best to address them.
Using a Lifecycle Assessment (LCA) audit to plug data gaps
Once data gaps have been found, the next priority should be conducting a lifecycle assessment (LCA). This process evaluates the environmental impact of a product throughout its lifecycle, starting from raw material extraction, offering a comprehensive understanding of its sustainability footprint.
Validating data sources to ensure reliability
It is crucial to validate data sources in order to create an accurate and verifiable representation of each product if SMEs want to use this within DPPs. This means assessing the credibility of third-party data suppliers, and ensuring the relevant standards underpin processes.
Making use of existing DPP solution providers
Due to both cost and complexity, building a new DPP solution won’t be an option for most SMEs, so they will need to seek out suitable partners who specialise in creating and implementing DPP solutions. Businesses should also consider whether the DPP solution can integrate with existing systems and how it creates an ongoing real-time picture of a product’s lifecycle.
Verifying systems with pilot programmes
Once a suitable DPP solution has been implemented, the next phase is to pilot the selected DPP solution with a small number of product lines. Through this phase, businesses can understand the real burden that a DPP implementation will place on their operations and update and scale their approaches to overcome this, ensuring they are ready for the final requirements once the delegated acts are released. Ultimately, successful compliance with the EU’s ESPR depends on a strategic, systematic approach to collecting, validating, and integrating product data throughout the supply chain.
While awaiting the release of the delegated acts brings some uncertainty, SMEs can simplify their journey to DPP compliance by focusing on actionable steps that can be taken ahead of time. Building a robust compliance strategy rooted in accurate data and trustworthy validation processes ensures alignment with ESPR requirements and drives enhanced sustainability and operational resilience for responsible businesses.