It was impossible to go through 2021 without hearing about the crisis afflicting global supply chains. Back in the first quarter of 2020 the pandemic triggered a catastrophic sequence of events that would ultimately impact how efficiently the world’s distribution networks operated.
As Covid-19 ripped across the world and instigated lockdowns across nations and industries, including manufacturing, many assumed that global demand would drop. As we know, the opposite happened, and the pandemic ended up supercharging the public’s appetite for goods as people ended up spending less on things like travel and eating out, preferring to make a beeline for shopping online. Retail sales for items like home improvements, home office setups, exercise machines et al all went through the roof.
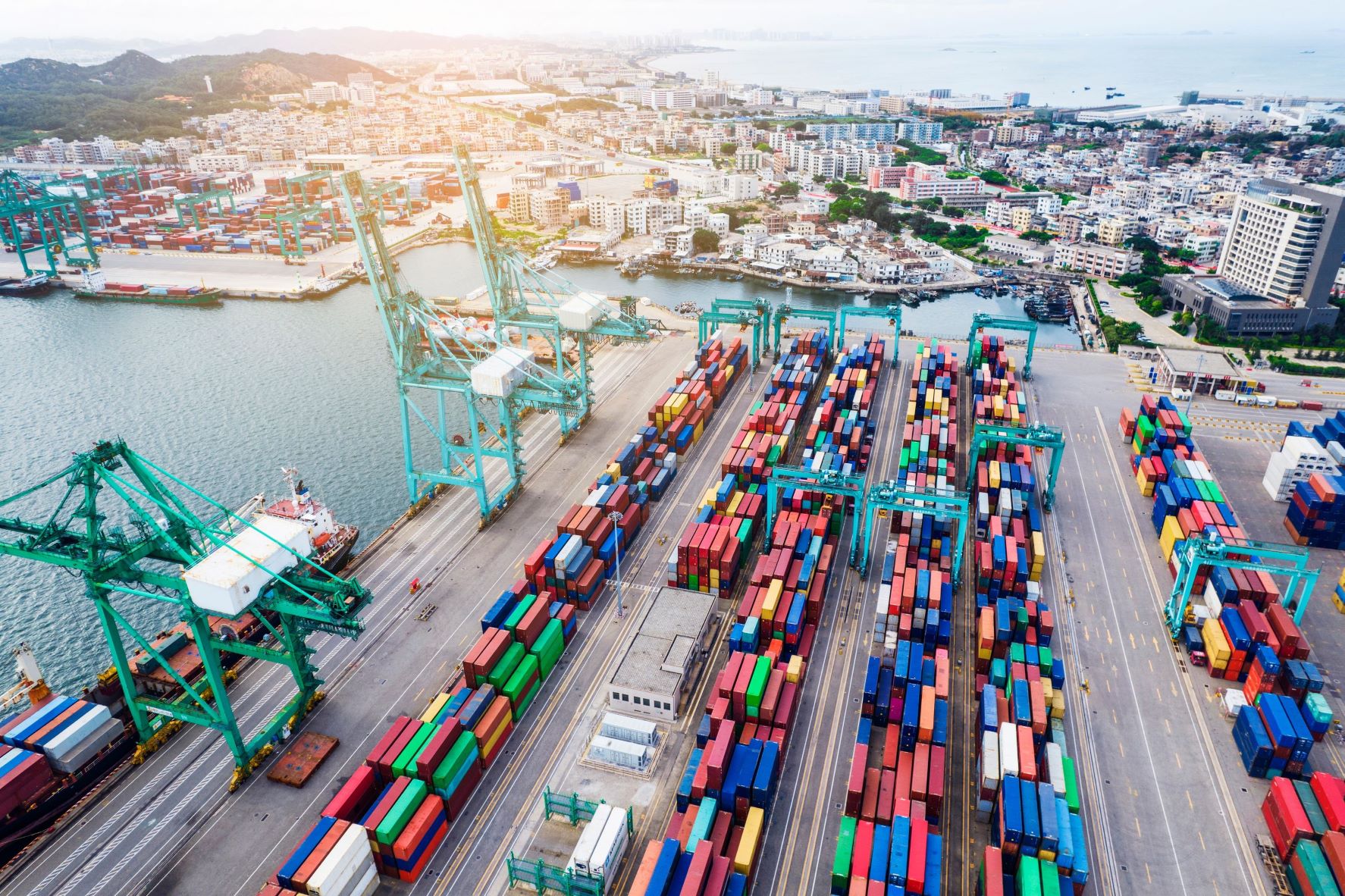
Even though production could be increased to meet the demand, sourcing parts or raw materials gradually became more difficult as parts of the world remained in differing states of shutdown. Transportation delays, temporary port closures, container shortages, absent and reduced workforces all conspired to destabilise the intricate supply lines that delivered items around the world. No industry escaped the carnage. Food supplies, on occasion, became sporadic. The availability of consumer goods was, for several periods, erratic. A lack of vital semiconductors caused upheaval across several industries, notably the automotive sector, with production lines around the world having to close for weeks at a time due to a lack of components.
The pandemic created the conditions for a perfect storm – collapsing all the efficiencies built into the world’s supply chains.
When our distribution systems do return to previous, and they will, operating smoothly once again, they are the epitome of precision collaboration, coordination and communication. These disruptions over the last two years have taught us some valuable lessons as well as bought us time to reflect on how products are produced and some of the insourcing and outsourcing requirements. The vulnerability of our supply chains has forced some re-evaluation on how we can improve things and whether technologies such as digital transformation, artificial intelligence or 5G could play a part in alleviating problems if they occurred again.
Data Analytics is an imperative in logistics
Today, data is driving the economy and disrupting how businesses operate. Data analytics in logistics is one of the domains that is experiencing widespread adoption and utilisation. The intricate structure of the supply chain makes logistics a perfect use case. Information can be extracted from numerous internal and external sources and touch-points along the chain i.e., traditional operational systems, sensors incorporated in vehicles, connected devices, suppliers, partners and customers. Valuable insights from the data will unlock efficiencies and optimise business.
Faster delivery at lower cost
With hundreds or even thousands of vehicles to manage daily, determining the optimum travel routes to minimise fuel or energy costs while ensuring deliveries are on-time is a major headache. Data analytics have been streamlining route optimisations – the process of determining the most cost-effective route with routing systems. Vast amounts of data are garnered from shipment information, vehicle capacity, holidays, road quality, traffic densities, crime hotspots and weather conditions which can be leveraged to calculate the most efficient route and stop sequences for fleets or to determine the most suitable modes of transportation (airplane, truck, train or ship) for long-distance routes, as well as the junction points to optimise the flow through the supply chain.
With real-time-routing solutions, on-the-fly data is collected and analysed to control delivery routes. Shippers, drivers and recipients can respond to real-time events and plan remediation alternatives. Routing intelligence balances changes in weather, traffic congestion and access to each destination with information about the availability and location of the receiver guiding drivers to the next best point of delivery to avoid an unsuccessful delivery attempt.
Not only do route optimisations systems help to reduce fuel and energy costs, overtime expenses, windshield and planning times they also improve the on-time arrival rates and fleet utilisations; the product being improved customer satisfaction.
Elements of AI are also finding their way into predictive analytics systems for intelligent transportation, route and demand planning. Big Data from the supply chain is analysed to identify patterns that help provide insights into every link of the supply chain.
Warehouses go beyond the role of just storing and handling goods. Smart warehouse systems utilise various interconnected technologies to form an ecosystem to automatically track where goods are received, identified, sorted, organised and prepared for shipment. Smarter warehouses automate the entire operation from supplier to customer. Data analytics, combined with automation, Internet of Things and artificial intelligence, provide enterprises with a bird’s eye view of the entire warehouse operation and relay back performance information related to the organisation and the delivery of goods. A smart warehouse improves productivity, efficiency, and accuracy while providing more flexibility and capability.
Lots of information can be collected from sensors to help keep track of parcel movements and detect abnormalities in the routes of forklifts. The monitoring of temperature and moisture levels will help companies plan the most efficient routes for picking perishable products and reduce wastage. While insights into inventory management reveal which parts of the warehouse are the busiest i.e., what products are in high demand and where should seasonal products should be stored to maximise full use of the floor space.
Furthermore, logistics operators have control over stock inventory at each warehouse based on historical and real-time data on customer demand and buying behaviours. An example where this may be useful is when popular products are ordered within a certain area. The closest warehouse to that region carries a higher inventory of that specific product to meet demand. Data-related technologies also enable companies to optimise the number, location and capacity of warehouses to minimise capital investment and ensure more efficient warehouse management.
Over the past few years, the logistics industry has benefitted from predictive analytics advances. Algorithms anticipate future behaviours based on historical data for predictive analytics to forecast supply and demand. Businesses can make more intelligent decisions about inventory planning, shipments, labour and capacity requirements. Logistics operators can generate reports on customer preferences, forecast demand and allocate workforce and resources accordingly. Predicting machine failures more accurately would make maintaining a site easier. Repairs or servicing can be factored in before they need to occur. Catching these issues ahead of time, maximises equipment uptime, reduces delays and rationalises operational costs.
Digitally transforming logistics for a better future
Global supply chains are lean and mean – and operate smoothly. While the pandemic exposed some of its fragilities embracing digital transformation has the potential to help logistics companies to take operations to another level – improving efficiencies, enhancing customer experiences as well better preparing us for unexpected events. Exploiting the data available is central to success as we digitally transform our way to a better future.
By Quy Le, Head of Delivery, FPT UK